Büyük eşanjörlerin kireç ve pas temizliğinde en kritik noktalar!
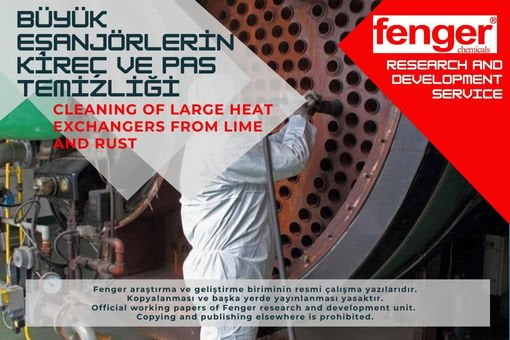
Büyük plakalı veya borulu ısı eşanjörlerinde (heat exchanger) kireç (scale) ve pas (rust) temizliğinde mutlaka göz önünde bulundurmanız gereken kritik noktaları; adım adım, hem teknik hem de uygulama boyutlarıyla özetledik;
1. Ekipman ve Ürün Uyumu
• Malzeme Analizi: Eşanjörün ana malzemesi (karbon çelik, paslanmaz çelik, bakır alaşımları vs.) ve iç kaplama/conta tipleri, kullanılacak kimyasal seçimini doğrudan etkiler.
• Kimyasal Uyumluluk: Asidik temizleyicilerin (fosforik/citrik asit bazlı) paslanmaz çeliğe zarar vermemesi, alkalin temizleyicilerin conta ve plastik parçaları aşındırmaması gerekir.
2. Ön İnceleme ve Numune Alma
• Kirlilik Seviyesinin Tespiti: Görsel muayene, ultrasonik kalınlık ölçümü veya metalurjik numune analiziyle kireç/pas tabakasının kalınlığı belirlenir.
• Su ve Tortu Analizi: İşletme suyu içindeki sertlik iyonları (Ca²⁺, Mg²⁺) ve askıda katı madde miktarı, önleyici yöntemlerin seçilmesi için yol gösterir.
3. Doğru Temizlik Kimyasalı ve Konsantrasyonu
Kir Tipi |
Kimyasal Tipi |
Konsantrasyon Aralığı |
İnhibitör Gereksinimi |
Kireç |
Fenger %5–15 Fosforik asit + inhibitör |
5–10 % |
%2–3 korozyon inhibitörü |
Kireç |
Fenger %5–10 Sitrik asit |
5–8 % |
%1–2 metal koruyucu katkı |
Pas |
Fenger %3–8 Hidroklorik asit + pas çözücü |
3–6 % |
Zorunlu (karbon çelik riski) |
Karışık |
Fenger Asit-karışım (fosforik + nitrit bazlı) |
%5–12 |
Yüksek inhibitör oranı |
4. İşlem Parametreleri
• Sıcaklık: 40–60 °C idealdir; yüksek sıcaklık hız kazandırır ama korozyonu artırır.
• Basınç ve Debi: Boru çapına göre eşanjörün tüm noktalarına kimyasalın ulaşabilmesi için minimum 1.5 bar basınç ve eşajör hacminin dakikada %10–20’si kadar debi önerilir.
• Süre: Kireç için genelde 4–8 saat, pas için 6–12 saat. Süre boyunca pH ve kirlilik seviyesi periyodik kontrol edilmelidir.
5. pH & Kir Yükü Takibi
• pH Ölçümü: Asit dozajı başlangıçta düşük tutulup, her 1–2 saatte pH ölçülerek asitle takviye edilir. pH stabil kaldığında çözünme tamamlanmış sayılır.
• Optik Bulanıklık Testi: Sistem çıkışından alınan numunenin bulanıklığı, özellikle pas/sediman varlığının görsel takibini kolaylaştırır.
6. Nötralizasyon & Durulama
1. Nötralizasyon: Temizlik sonrası sirkülasyona %1–2’lik sodyum hidroksit (NaOH) veya sodyum karbonat (Na₂CO₃) çözeltisi verilerek pH 7–8’e çıkarılır.
2. Durulama: En az 2–3 tam hacim su ile (işletme suyu yerine mümkünse deiyonize su) kimyasal kalıntıları tamamen uzaklaştırın.
7. Korozyon İnhibitörleri ve Pasivasyon
• Pasivasyon Aşaması: Durulamadan hemen sonra %0.1–0.3 nitrit/benzoat bazlı inhibitör verilerek metal yüzeyde koruyucu ince film oluşması sağlanır.
• İzleme: Son 1 hafta boyunca haftalık ultrasonik kalınlık ölçümleri ile korozyon hızı takip edilmelidir.
8. Güvenlik & Çevresel Uyum
• KKD Kullanımı: Asit/baz korozif etkisine karşı eldiven, yüz siperi, kimyasal önlük, uygun havalandırma zorunludur.
• Atık Yönetimi: Kullanılmış kimyasal ve durulama suları, nötralize edildikten sonra çevre izinlerine uygun depolama/bertaraf tesislerine gönderilmeli; biyolojik olarak parçalanabilir ürünler tercih edilmelidir.